КамАЗ рассказал, как импортозамещал комплектующие для флагмана КамАЗ К5. За год пришлось локализовать производство 135 деталей
После ухода многих иностранных брендов из России КамАЗ, ГАЗ, АвтоВАЗ и другие производители отечественных автомобилей столкнулись с серьезным дефицитом комплектующих. Например, КамАЗу пришлось в довольно короткий срок — около года — импортозаместить 135 комплектующих для грузовиков пятого поколения (КамАЗ К5). Руководитель проекта «Аутсорсинг производства «КАМАЗа» Сергей Мандрик рассказал, что это были за системы.
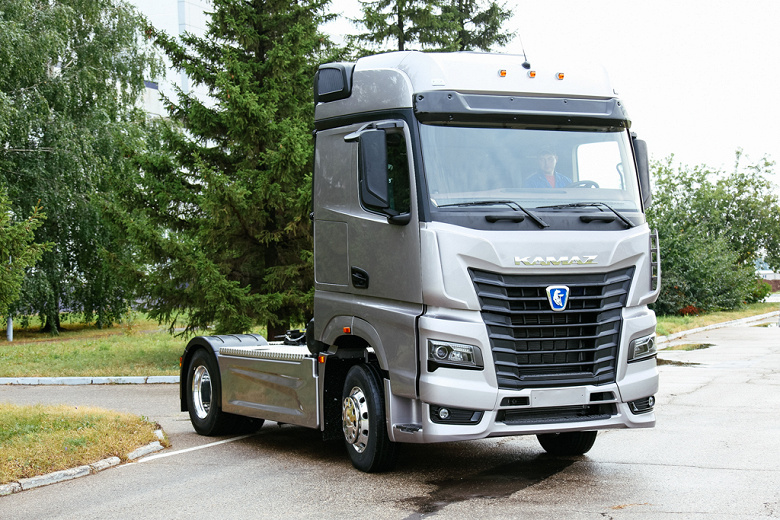
Оказывается, на КамАЗ К5 помимо крупных деталей вроде постов и коробки передач устанавливали много всего другого импортного. Например, импортной была климатическая система, элементы обивки, термошумоизоляция, воздухозаборник, фильтры, сложные литые кронштейны, замки, заглушки и уплотнители. И вот все это пришлось замещать в сжатые сроки. Быстрее всего справились с мелким крепежом и заглушками, а самой сложной деталью оказался кронштейн рулевой колонки.
»С его исполнением мы определились совсем недавно, это очень сложное, ажурное, тонкостенное литое изделие с особыми требованиями к конструкции. Пришлось обойти немало поставщиков и даже привлечь экспертов по литью из других стран для сравнительного анализа. В конце концов мы увидели, что и в России достаточно опытных специалистов по этому вопросу. Сейчас поставщик из Санкт-Петербурга завершает технологическую подготовку производства, и, по расчетам, к концу второго квартала этот кронштейн тоже станет полностью российским», — рассказал Сергей Мандрик.
А вот пример того, как в результате работ по импортозамещению в России появился совершенно новый материал.
»Прежде мы закупали в Германии смолонаполненную базальтовую вату — основу термошумоизоляционных матов для К5. Чтобы компенсировать импорт, нам пришлось запустить НИОКР в сотрудничестве сразу с несколькими предприятиями. Сначала вышли на компанию, которая добывает базальт, крошит его, плавит и растягивает в волокна. Затем решили задачу насыщения базальта поликонденсационной смолой с сохранением однородной структуры. В итоге за год мы получили новый для отечественного рынка материал», — пояснил Сергей Мандрик.
© iXBT